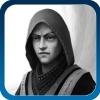
Создайте учётную запись или войдите для комментирования
Вы должны быть пользователем, чтобы оставить комментарий
Создать учётную запись
Зарегистрируйтесь для создания учётной записи. Это просто!
Зарегистрировать учётную запись
Вы должны быть пользователем, чтобы оставить комментарий
Зарегистрируйтесь для создания учётной записи. Это просто!