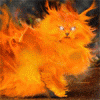
Броненосец к РЯВ с послезнанием и деньгами
Автор
Фрерин,
Создайте учётную запись или войдите для комментирования
Вы должны быть пользователем, чтобы оставить комментарий
Создать учётную запись
Зарегистрируйтесь для создания учётной записи. Это просто!
Зарегистрировать учётную запись